This process is used to derive a recipe of materials that, as a mix, has a desired oxide formula. In Insight-live we do it by setting up two recipes, side-by-side. One is the target-to-be-matched and the other is the batch recipe being built.
Help topic #587 offers a step-by-step lesson to do a formula-to-batch calculation, that may be the most practical way to learn this.
It is important to recognize the limitations of this:
- Theoretically, many different recipes can be calculated to produce the same chemistry, depending on the materials chosen to source each oxide. However in practice, you likely have a limited selection of materials (especially frits). That sometimes means you may have to be satisfied with a less-than-perfect match.
- There may be no combination of materials you want to use that can match the chemistry of your target formula. For example, a formula may demand high enough levels of B2O3, BaO or Li2O that no available frit can supply them without oversupplying other oxides. This can require the need to employ expensive or difficult or toxic raw materials (e.g. Gerstley Borate, lithium carbonate, barium carbonate).
- Theoretically, two different recipes having the same chemistry should fire the same. However in practice, there will be differences in the mineralogy and physics of the materials that also affect melting (e.g. sourcing chemistry from a frit vs. raw materials, from high-melting vs. low-melting raw materials).
- If the accuracy and availability of chemistry information for materials is in question the likelihood of a good match is reduced.
Create a Target
First, use the Add a Recipe button (in the Recipe Manager). Use the Done Editing button to save it and leave edit mode.
If your target is a chemical analysis
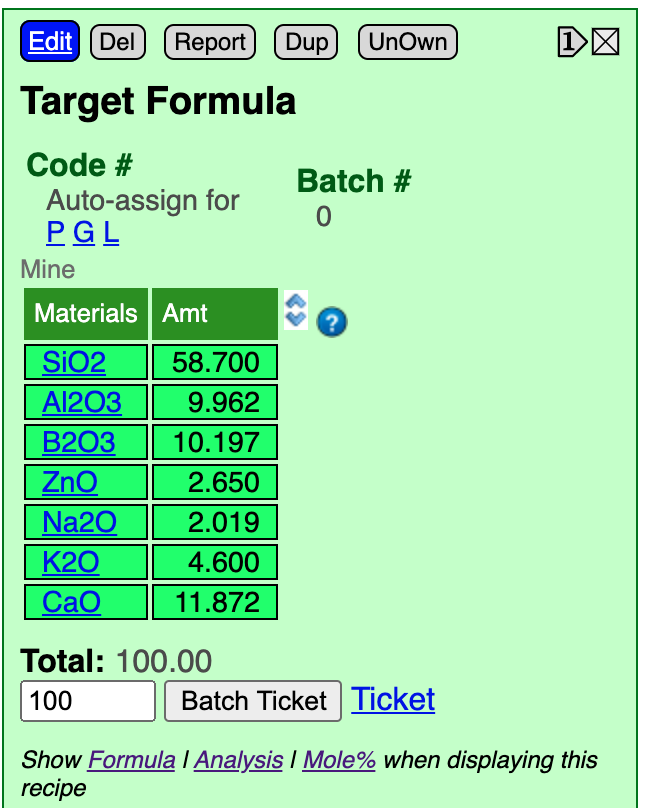
Just enter it as a recipe. Insight-live recognizes the oxides and calculates the equivalent formula.
This might seem strange since recipes, by definition, are lists of materials and weights. But Insight-live not only knows oxides as molecules in formulas and analyses but also as theoretical materials (as if the oxide were available as a 100% pure ceramic powder with zero LOI). Of course, no such pure materials exist, but this concept enables us to create these targets.
If your target is an oxide formula
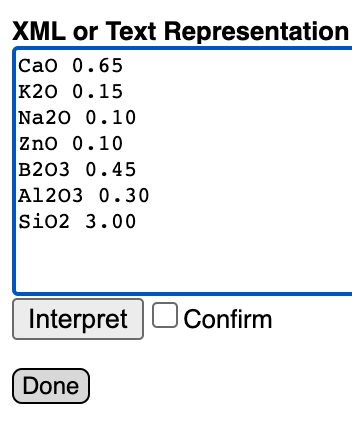
Use the XML and Text Import/Export button at the bottom of a recipe panel to show the import dialog. This is normally used to paste recipes into Insight, but it can recognize a formula and treats it specially: The formula is converted to a chemical analysis and entered automatically into the recipe of the current panel. The analysis that Insight creates will calculate to the formula that you entered.
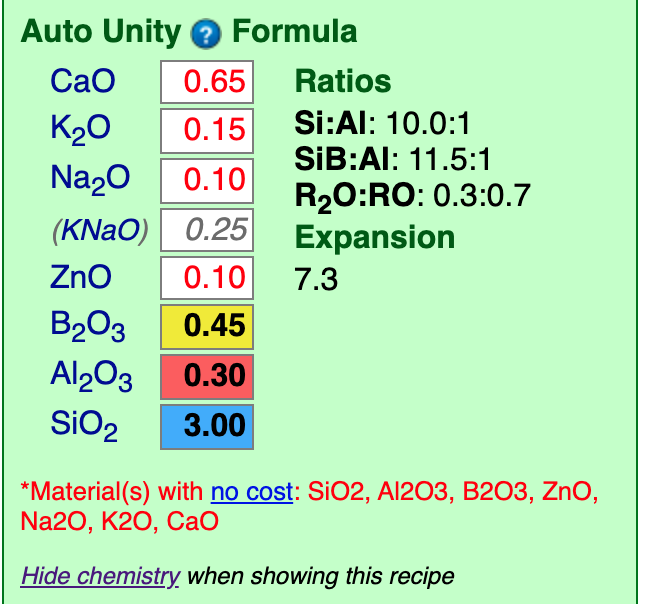
No matter which of the methods you use to enter the target, it will calculate as shown here. One possible issue: If the formula you enter is not unity, then it will not look the same as this one.
The target recipe should be named, code-numbered, notes and other documentation added and kept permanently. It is often valuable to establish links between a target and material batch recipes derived to match it.
Material Chart
The Material Chart button in the Materials Manager will display a chart of all materials you manage, this makes it easier to choose the right one to supply the oxide needed. Typically you will display this whenever there is a doubt about which material to use to supply an oxide.
When done click the icon on the upper left.
As you develop knowledge about your materials you will not need this chart, it is usually obvious which material to use to source a needed oxide.
Unity or Non-Unity Calculation?
Non-Unity
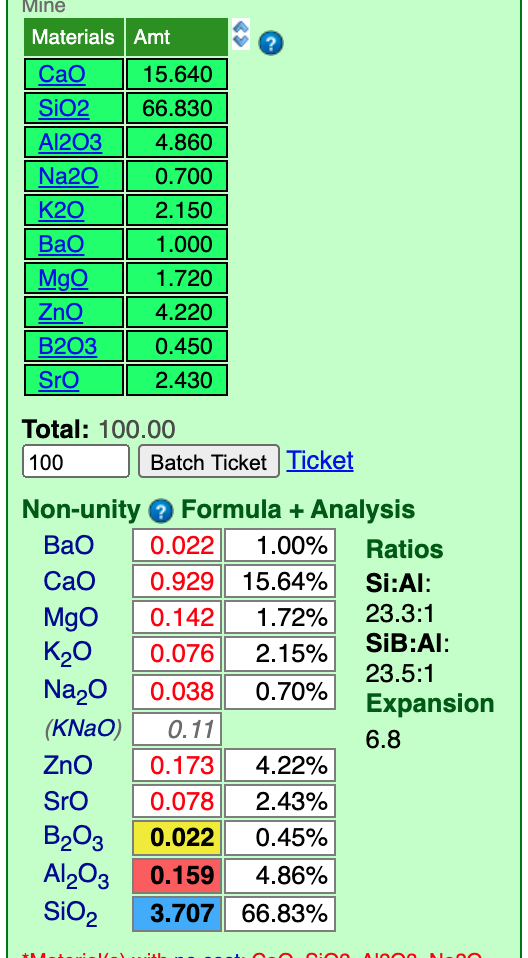
When the calculation type for a recipe is set to Non-unity (as shown here) Insight does not retotal the formula to any kind of unity. That means that changes made to the amount of a material in the recipe only change the values of the oxides that it contributes. This is ideal for building a batch and tuning its chemistry to match a target.
Setting the target at non-unity offers two other advantages. First, the individual values are larger, so you are not working as much with fractional additions. In fact, it is sometimes helpful to retotal the percentage analysis entered to 1000 instead of 100 just to generate larger formula numbers (for easier matching with integer material amounts). A second advantage is that Insight shows the formula to three decimals for non-unity. This enables closer matching of oxide amounts.
Unity
Although it is possible to build a batch recipe while it recalculates to unity, this method is normally only used to make minor changes to a recipe. For example, suppose you substitute calcium carbonate for wollastonite. In the screen-shot below it is evident that this changes all the oxide values, even though wollastonite only contributes two, SiO2 and CaO.
To match the chemistry back up:
- Turn on calculation mode.
- Enter "1" into the Increment/decrement box.
- Trim the wollastonite upward until the CaO matches the original.
- Trim the kaolin downward until the Al2O3 matches.
- Trim the silica downward (a lot) until the SiO2 matchs.
Formula to Batch (Mole%)
Some people prefer to use a %Analysis when doing "from-scratch" chemistry-to-batch calculations. The Mole% method has a distinct advantage: It represents the fired product with no LOI. This is most important when the mix of materials being employed to source the oxides does have an LOI.
When using this method (rather than No-Unity) you collect all the materials needed to source the oxides and then juggle the recipe as-a-whole while watching the effect on the formula as-a-whole.
The screenshot below shows an example (the oxide numbers have not been perfectly matched, more work is needed).
Link Batch to Target
It is a good idea to link the batch recipe to the target. Close all recipes except the batch.
- Find the target in the Recipe Manager panel and click its checkbox.
- Select the link reason
- Click or tap the Link button.
Here is an example of how the link displays (down the batch recipe panel). Since we neglected to codenum the target it is referred to as "UnNumbered". Then its title is shown along with the type of link (they are the same because we named the target as "Target Chemistry").
Compared to Desktop Insight
Insight-live sees chemistry-to-batch calculations as a guided process where you determine how materials share in supplying oxides. Choices you make during the process must be tempered by knowledge of how the materials will affect the physical slurry and its working and drying properties (e.g. if there is not enough clay in a glaze it will not suspend in the bucket or harden on drying). Users of Insight-live are much more likely to be using real-world materials rather than theoretical ones in calculations, such materials have complex formulas and supply many more oxides. That means compromises must be made between mathematics and what is practical. A big advantage of Insight-live is that material information is much more at-hand than with desktop Insight.